Preventing Crystallization in Spray Foam Equipment
- Jeromy Svec
- Dec 2, 2024
- 5 min read

Spray foam is used across a variety of construction projects to provide a seamless barrier that insulates and protects. However, one pesky problem that can disrupt this process is crystallization. This issue can cause headaches for contractors, leading to equipment malfunctions and poor-quality applications.
Preventing crystallization in spray foam equipment can be challenging, even for the most seasoned professionals. To help you do the job right, we’ll explore how crystallization occurs, its impacts, and how to avoid it. Whether you’re an experienced professional or new to the world of spray foam, you can benefit from these insights to help your equipment run smoothly and effectively.
What Is Crystallization in Spray Foam Equipment?
Crystallization is a common issue affecting spray foam equipment that occurs when the A component (isocyanate), used in creating spray foam, begins to solidify or form crystals. These crystals can lead to blockages and clogs in the equipment, disrupting the flow of foam and affecting the application process. Addressing crystallization early can prevent disruptions to your operations and keep your equipment in top working condition.

Understanding the Causes of Crystallization
Several factors contribute to spray foam equipment crystallization, making it more difficult to achieve quality results.
Environmental Factors
Environmental conditions play a role in causing spray foam equipment crystallization. Temperature fluctuations, particularly exposure to cold temperatures, can lead to the solidification of foam components. High humidity levels can also accelerate crystallization by introducing moisture into the mixtures, disrupting their stability and flow.
Storage and Handling
Proper storage and handling of spray foam components prevent crystallization. Isocyanate exposed to air or contaminated during storage is more likely to crystalize. Incorrectly sealed containers or transfers between containers can also introduce impurities that serve as nucleation points for crystal formation. Storing materials in a controlled environment and handling them with care is essential to maintaining integrity.
Maintaining Proper Spray Foam Component Ratios
Improper ratios in the spray foam can also lead to crystallization. If the ratios are incorrectly calibrated, the mixture may become unstable, increasing the risk of crystal formation. Follow precise instructions, regularly checking the equipment calibration for consistent, proper mixing of components to prevent crystallization.
The Impact of Crystallization on Equipment Performance
The consequences of crystallization in spray foam equipment can be severe, affecting equipment performance and spray foam application quality.
Equipment Blockages and Downtime
Crystallization can lead to blockages within spray foam equipment, particularly in hoses and nozzles. These obstructions prevent the smooth flow of foam, resulting in uneven application or complete cessation of output.
Consequently, the equipment may require frequent stops for cleaning and maintenance, leading to increased downtime. This interruption slows project timelines and increases labor costs, as additional time and resources are spent on addressing the issue.
Degraded Foam Quality
Another major impact of crystallization on equipment performance is the degradation of foam quality. When spray foam components crystallize, they can cause inconsistency in the mixture and application, resulting in poor adhesion and uneven texture. The defective foam application can compromise the insulation properties, reducing energy efficiency and potentially leading to costly repairs or replacements. Prioritizing high-quality foam output maintains the integrity and durability of your construction projects.
Increased Maintenance Costs
Crystallization-related problems require regular maintenance and cleaning of affected equipment, escalating maintenance costs. Frequent breakdowns necessitate the replacement of parts such as hoses, nozzles, and filters, which can be costly over time.
Additionally, addressing crystallization may require specialized cleaning agents and techniques to dissolve and remove the crystal formations, further adding to expenses. Investing in preventative measures can mitigate these costs and extend your spray foam equipment’s service life.
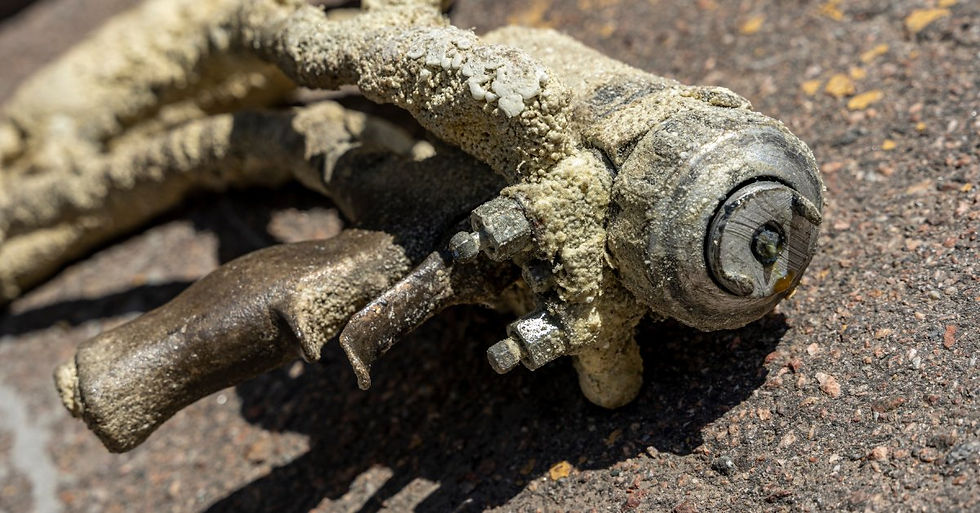
Preventative Maintenance Tips To Avoid Crystallization
Preventative maintenance can curtail crystallization in spray foam equipment . Keep the tips below in mind.
Store components properly: Always keep spray foam chemicals in a temperature-controlled environment to prevent exposure to extreme cold or heat. Tightly seal containers to avoid contamination and moisture ingress.
Regularly clean equipment: After each use, thoroughly clean hoses, nozzles, and other equipment to remove residue that may solidify and form crystals over time.
Monitor environmental conditions: Before and during application, check the temperature and humidity levels to confirm they’re within the recommended range for optimal spray foam performance.
Use correct formulations: Strictly adhere to the recommended chemical ratios to maintain a stable mixture and prevent imbalances that can lead to crystallization.
Inspect equipment frequently: Conduct regular spray foam equipment inspections to identify early signs of crystallization, such as blockages or inconsistent flow, and address them promptly.
Implement routine maintenance: Establish a maintenance schedule that includes checking and calibrating equipment for precise component mixing, reducing the risk of crystal formation.
Invest in quality components: High-quality spray foam products and parts are less prone to issues with crystallization, providing more reliable performance.
DIY Versus Professional Application
When managing crystallization in spray foam equipment, a key consideration is whether to tackle it yourself through DIY methods or hire professional services. Each approach comes with its own advantages and potential drawbacks.
DIY Approach
The DIY approach can offer cost savings and immediate access to problem-solving solutions without waiting for professional assistance. However, you must understand the equipment’s mechanics and the crystallization process to avoid exacerbating the problem.
Experienced operators familiar with the intricacies of equipment should find that performing routine maintenance and directly addressing crystallization can be an efficient way to quickly mitigate issues. DIY maintenance involves regularly cleaning components, maintaining optimal storage conditions, and adhering to recommended chemical formulations.
Professional Services
Hiring professionals to manage crystallization and perform maintenance on spray foam equipment can provide peace of mind, especially for those less familiar with technical details. Professionals have specialized tools and expertise to handle complex issues. Their service will keep the equipment maintained and operating at peak efficiency.
While this option may incur higher costs compared to DIY methods, professional service often results in improved longevity and reliability with fewer unexpected breakdowns. Moreover, professional services may offer comprehensive inspections and provide solutions that a DIY approach can overlook.
Making the Right Decision
Selecting between DIY and professional services hinges on factors such as expertise, budget, and project scale. Enlisting professional assistance may be the best choice for large-scale operations or when precision is critical. Conversely, those with technical know-how and the time to dedicate to maintenance may find DIY methods adequately effective in managing crystallization and keeping equipment in top shape.
Taking the Guesswork Out of Your Spray Foam Application
Preventing crystallization in spray foam equipment has its challenges, but by understanding the causes and implementing preventative measures, you can maintain high-quality results. With these strategies, you can maintain the integrity of your spray foam applications so your equipment serves you reliably for years to come.
Are you in need of spray foam equipment that won’t let you down when it matters most? Hand Crafted Hose Company has everything you need to get the job done right. Whether you’re a professional or looking for a DIY solution, you can rely on spray foam heated hose to simplify application so you can get on with construction.